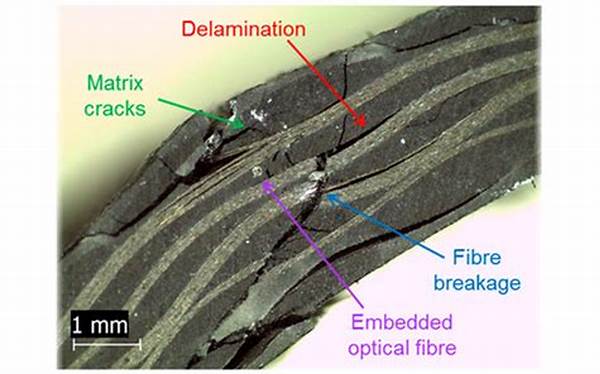
**material Defect Fatigue Impact**
In a world where the integrity of materials determines the safety and longevity of countless structures and products, understanding the material defect fatigue impact is imperative. Imagine a scenario where minute flaws in materials lead to catastrophic failures, causing widespread harm and financial loss. It is a silent menace lurking within the very fabric of materials. By recognizing the profound effects of these defects, we can take proactive measures to enhance durability, ensure safety, and drive innovation. This is not just about physics; it’s about preserving lives and investments. Let’s delve deeper into the significance of acknowledging and addressing the material defect fatigue impact.
Read Now : Certified Brake Testing And Validation Services
Understanding Material Defect Fatigue Impact
The material defect fatigue impact is a critical concern that manifests when materials deteriorate over time due to cyclical loading. These defects are often microscopic and initially go unnoticed. However, their impact is massive, as they lead to premature material failure. Imagine the consequences in critical applications, such as aerospace or civil engineering, where even the smallest defect can result in catastrophic failure. This is why understanding and mitigating the impact is essential. The ongoing research and technology in detecting and countering these defects can save industries exorbitant amounts of money and prevent life-threatening incidents. Investing in advanced diagnostics and material science research will pave the way for safer, more durable materials.
Material defect fatigue impact is not merely a technical term; it represents a challenge that the modern world must overcome. It involves addressing both the microscopic and macroscopic levels of material integrity. By prioritizing robust testing and acknowledgment of the potential impacts, industries can innovate with confidence, knowing that their products will withstand the test of time. The conversation doesn’t end here—it’s just the beginning of a larger narrative focused on safety, innovation, and sustainability.
Preventing Material Defect Fatigue Impact
1. Rigorous Material Testing: Employing comprehensive testing methods is crucial to understanding the material defect fatigue impact. It allows for early detection of vulnerabilities before they escalate.
2. Investment in Research: Funding material science research is paramount. It could lead to breakthroughs in how we identify and counteract material defect fatigue impact.
3. Advanced Technology Adoption: Embrace cutting-edge technologies for real-time monitoring. This technology can identify the material defect fatigue impact promptly.
4. Quality Control Enhancements: Implement more stringent quality control processes to catch the material defect fatigue impact before materials reach the market.
5. Educational Initiatives: Educate engineers and designers about the material defect fatigue impact, ensuring they incorporate this knowledge into their projects.
The Need for Comprehensive Solutions
The material defect fatigue impact is an urgent call for comprehensive solutions. This challenge requires a multifaceted approach, combining advances in material engineering, real-time monitoring systems, and a shift in industry culture toward proactive prevention rather than reactive measures. As industries increasingly rely on complex materials, so does the potential for unnoticed defect accumulation. Recognizing this calls for a united effort among all stakeholders to collectively prioritize defect identification as a critical factor in material design and utilization.
The financial and human safety stakes are simply too high to ignore. Investing in a robust framework to counter material defect fatigue impact is not just an option but a necessity. It means committing to research and development that focuses on innovative material solutions and investing in state-of-the-art testing and monitoring systems. Doing so fosters a culture of diligence and foresight in material usage, ensuring that every structure and component not only meets but exceeds safety standards.
Read Now : Repairing Ignition Wiring Issues
Strategies to Mitigate Material Defect Fatigue Impact
Adopting a forward-thinking mindset is vital in countering the material defect fatigue impact. Manufacturers must implement robust strategies designed to identify, analyze, and repair potential defects before they escalate. Leveraging artificial intelligence and machine learning can significantly enhance predictive maintenance capabilities, allowing for early intervention strategies that minimize the risk of catastrophic material failure.
Developing more resilient materials through cutting-edge research and innovative manufacturing processes can further reduce susceptibility to material defect fatigue impact. This effort should be combined with a comprehensive review of existing standards and practices within industry sectors, encouraging continuous improvement and adaptation in line with the latest advances in technology and understanding of material behaviors.
Impact on Structural Integrity
Consequences of Ignoring Material Defect Fatigue
Ignoring the material defect fatigue impact can have dire consequences for structural integrity and safety. The progression from a small, undetected flaw into a critical failure could mean the difference between safe operation and disaster. In an era of unprecedented technological reliance, a single material defect can cascade into a significant incident impacting lives and economies.
Taking a proactive stance on identifying and mitigating these defects is imperative in building a resilient future. Engineers, researchers, and policymakers alike must leverage existing technology and push the boundaries of material science to preemptively address potential failures. This not only safeguards structures and people but also significantly reduces the long-term costs associated with repairs and liability.
Importance of a Proactive Approach
A proactive approach in handling the material defect fatigue impact not only ensures longer material life but also enhances the overall reliability and trust in engineering practices. This approach involves fostering a culture of vigilance from the moment of material selection through its lifecycle, incorporating constant monitoring and innovative repair strategies when necessary. By anticipating where defects might occur, industries can effectively prevent material failures, ultimately leading to safer environments and more sustainable practices.
Conclusion and Call to Action
Emphasizing the Urgency for Collaboration
The material defect fatigue impact represents a critical challenge that transcends individual sectors, necessitating wide-scale collaboration among industries, governments, and research institutions. By pooling resources and knowledge, a holistic approach can be developed, integrating the latest technological advancements with traditional engineering principles. This collaboration is pivotal to effectively addressing and mitigating the impacts of material defects proactively.
Final Thoughts
In conclusion, understanding the material defect fatigue impact and its implications is vital for developing safer, more reliable materials. Investment in cutting-edge technology and fostering an industry-wide culture of proactive maintenance can significantly mitigate risks. As we advance, the focus must remain on integrating innovation with traditional methodologies, ensuring that the integrity of materials, and consequently, the safety of individuals, remains paramount. Your role in acknowledging and acting upon this concern could make all the difference in safeguarding our future infrastructure.