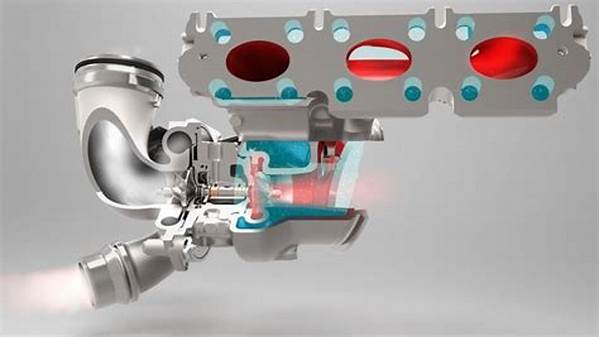
“advanced Materials For Turbocharger Durability”
In today’s competitive automotive industry, enhancing the durability of turbochargers is crucial. Turbochargers are vital for optimizing engine performance and reducing emissions. However, these components face extreme conditions, including high temperatures and pressures. Utilizing advanced materials for turbocharger durability is not just a necessity but a strategic move to ensure longevity and reliability. By investing in cutting-edge materials, manufacturers can significantly reduce failure rates and maintenance costs, paving the way for more sustainable and efficient automotive solutions.
Read Now : Emergency Roadside Recovery Service
High-Temperature Alloys: A Game Changer
The introduction of high-temperature alloys marks a revolutionary step in improving turbocharger durability. These materials not only withstand the intense heat generated by engine exhaust gases but also maintain strength over prolonged use. The usage of such advanced materials for turbocharger durability enhances the lifespan of turbochargers, providing cost savings over time. With innovations in metallurgical engineering, these alloys promise to address the persistent issues of thermal fatigue, oxidation, and wear.
Furthermore, the ongoing research and development in high-temperature alloys ensure that the future holds promising advancements for automotive technology. By choosing to integrate these advanced materials for turbocharger durability, manufacturers can stay ahead in the market, offering products that stand the test of time and harsh operating environments. The sustainability angle adds an extra layer of appeal, aligning with global efforts to reduce carbon footprints.
Composite Materials: The Future of Durability
Composite materials bring a blend of strength, lightweight properties, and resistance to environmental damage, making them indispensable in the quest for advanced materials for turbocharger durability. These materials, created by combining two or more constituent materials, offer benefits that traditional materials cannot match. They lead to less wear and tear, thus prolonging the turbocharger’s operational life.
Another appealing feature of composite materials is their ability to be engineered for specific performance requirements, thus tailoring solutions to exact needs. By investing in the research and application of composite materials, the automotive industry stands to make significant strides in the realm of turbocharger technology, ensuring robust performance in increasingly demanding environments.
Ceramic Matrix Composites: Revolutionizing Durability
Ceramic matrix composites (CMCs) have emerged as a frontrunner in the creation of advanced materials for turbocharger durability. These materials provide solutions by combining light weight with exceptional thermal and mechanical properties. This unique combination results in improved efficiency and reduced component weight. CMCs are excellent at resisting thermal shock – a critical factor for turbochargers subject to rapid temperature changes.
As the auto industry anticipates tougher emissions standards, CMCs offer a pathway to meet these demands without compromising on performance. Investing in these materials now can deliver unparalleled benefits in turbocharger reliability, fuel efficiency, and compliance with future regulations, pushing the boundaries of what is possible in the automotive sector.
Fueling Innovation: The Role of R&D
Continuous research and development play a pivotal role in advancing advanced materials for turbocharger durability. R&D efforts focus on enhancing the properties of materials to endure harsh operating conditions, thus leading to innovations that set new standards for the industry. With R&D, manufacturers can unravel new potential of existing materials while discovering novel materials to revolutionize turbocharger durability.
Moreover, R&D encourages collaboration across sectors, fostering innovation and knowledge-sharing. Such synergies can lead to breakthroughs that not only improve turbocharger performance but also contribute to the sustainability of the automotive industry as a whole.
Lightweight Metals: The New Era
Transforming Durability with Lightweight Metals
The introduction of lightweight metals presents a new era in the development of advanced materials for turbocharger durability. These metals, such as titanium and magnesium alloys, offer high strength-to-weight ratios that enhance performance while reducing overall vehicle weight. This aspect becomes crucial as automakers strive to meet stringent fuel efficiency standards.
By embracing lightweight metals, manufacturers can achieve a balance between performance, durability, and efficiency. These materials allow for the creation of innovative designs that are not only lighter but also more robust. As consumer demand grows for vehicles that perform efficiently without sacrificing robustness, lightweight metals remain an essential focus in material innovation.
Read Now : Automated Fleet Maintenance Scheduling
Additionally, the reduced weight from these metals means less strain on engine components, translating into a longer lifespan for turbochargers. Through such strategic adoption of advanced materials for turbocharger durability, the auto industry can enjoy an era where high performance does not come with the penalty of excess weight or reduced durability.
Titanium Alloys: Strength Measured in Featherweights
Titanium alloys stand out in the arena of advanced materials for turbocharger durability, thanks to their exceptional strength-to-weight ratio. These alloys offer unmatched performance under high stress, ensuring that turbochargers can endure the extreme operational demands they face. Their inherent corrosion resistance further enhances their appeal, contributing to longevity.
Incorporating titanium alloys into turbocharger components signifies a leap towards efficiency, as vehicles benefit from reduced weight and increased fuel economy. Consumers are demanding more eco-friendly options, and the use of advanced materials like titanium in turbocharger design directly answers this call, paving the way for a greener automotive industry.
By rethinking material usage and focusing on sustainable, efficient technologies, embracing advanced materials for turbocharger durability can help redefine the landscape of automotive engineering. Manufacturers who prioritize these innovations are better positioned to lead the charge toward a more sustainable and efficient future.
Summary: Beyond Conventional Materials
The era of conventional materials is giving way to advanced alternatives, setting a new benchmark for turbocharger performance. By turning towards advanced materials for turbocharger durability, the automotive industry is witnessing radical improvements in both technology and sustainability. This pivot signifies not just a change in materials, but a shift in the paradigm of vehicle design.
The adoption of high-temperature alloys, composite materials, and lightweight metals underscores an industry-wide commitment to innovation and excellence. Turbochargers equipped with these materials boast enhanced life spans, resistive properties, and efficiency. In doing so, they contribute to the larger goal of reducing automotive emissions and environmental impact, aligning with global challenges and regulatory standards.
Manufacturers need to recognize the benefits that advanced materials for turbocharger durability bring and act accordingly to stay ahead of emerging trends. The investment in these materials is an investment in the future, where the balance between performance, durability, and sustainability defines the new norm in automotive excellence.