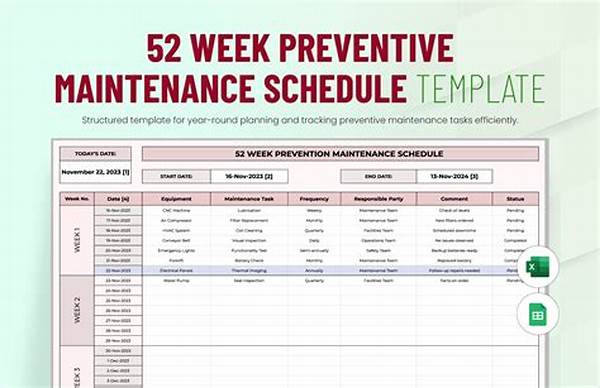
“optimizing Preventive Maintenance Schedules”
In an increasingly competitive marketplace, optimizing preventive maintenance schedules is not just an option—it’s a necessity. Imagine a future where your company operates seamlessly with minimal downtime, saving costs and enhancing productivity. This future isn’t far off. It’s achievable with a strategic approach to preventive maintenance. Every moment your machinery remains unproductive is a missed opportunity, a cost that could have been avoided. Don’t let inefficiency be your silent competitor. It’s time to take control of your maintenance strategy, ensuring that your operations run smoothly without unexpected interruptions. Let’s dive into why optimizing preventive maintenance schedules is the key to unlocking unparalleled efficiency and savings.
Read Now : Tailored Repair For European Vehicles
The Importance of a Smart Maintenance Strategy
Adopting a smart maintenance strategy is crucial for any thriving business. Implementing a system for optimizing preventive maintenance schedules not only extends the lifespan of your machinery but also boosts operational efficiency. By anticipating potential failures before they occur, businesses can significantly reduce unexpected downtimes, which are often costly and disruptive. A well-optimized preventive maintenance schedule allows companies to allocate resources more effectively, ensuring that maintenance teams focus on the most crucial tasks at the right time.
Moreover, optimizing preventive maintenance schedules enables data-driven decision-making. By analyzing historical data and monitoring real-time performance, businesses can fine-tune their maintenance activities, increasing the reliability of their equipment. This proactive stance not only saves time and money but also enhances the overall safety conditions within the workplace, safeguarding employees and reducing liability risks. In essence, a strategic approach to maintenance is no longer a luxury but an operational imperative.
The journey towards optimizing preventive maintenance schedules is also about staying ahead of the competition. As technological advancements continue to reshape industries, those who neglect their maintenance strategies may find themselves lagging. Embracing a forward-thinking approach to maintenance not only prepares your business for unforeseen challenges but also positions it at the forefront of innovation and operational excellence. Don’t wait for an equipment failure to realize the importance of this strategy; act now and secure the future of your business.
How Optimized Maintenance Saves Costs
1. Minimized Downtime: Optimizing preventive maintenance schedules significantly reduces unexpected downtimes. By having a preemptive approach, businesses avoid the costly disruptions that can occur, leading to continuous operational flow and resultant financial savings.
2. Enhanced Equipment Longevity: By diligently maintaining equipment through optimized schedules, companies can extend the lifespan of their machinery. This means fewer replacements and repairs, ultimately leading to substantial cost reductions over time.
3. Resource Efficiency: Allocating maintenance resources efficiently is a result of optimizing preventive maintenance schedules. By targeting specific needs at optimal times, businesses make better use of manpower and materials, reducing wastage, and maximizing ROI.
4. Improved Productivity: An optimized maintenance schedule ensures machinery operates at peak performance, contributing to higher productivity levels. This leads to an increase in output without the additional costs associated with unexpected machinery failures.
5. Predictive Savings: Optimizing preventive maintenance schedules incorporates predictive maintenance tactics, leveraging data analytics to foresee potential breakdowns, allowing proactive steps to be taken that save costs in repairs and downtime.
Proactive versus Reactive Maintenance
The contrast between proactive and reactive maintenance is stark, particularly when considering the long-term benefits of optimizing preventive maintenance schedules. Proactive maintenance, which encompasses preventive and predictive strategies, focuses on preempting equipment failures. This approach is built on foresight and strategic planning, enabling businesses to anticipate and prevent potential issues before they manifest. By doing so, companies not only ensure the smooth operation of their machinery but also safeguard against unexpected financial expenditures.
Conversely, reactive maintenance addresses equipment failures after they have occurred, often resulting in costly repairs and prolonged downtimes. This approach is inherently less efficient because it involves responding to emergencies that disrupt regular operations. The unpredictability associated with reactive maintenance can also lead to stress and resource misallocation, affecting overall business performance negatively. Optimizing preventive maintenance schedules, therefore, becomes a linchpin in transitioning from a reactive to a proactive maintenance posture.
Furthermore, adopting a proactive maintenance strategy aligns with the broader organizational goals of sustainability and efficiency. By reducing unnecessary waste and conserving resources, optimizing preventive maintenance schedules contributes positively to both the environment and the company’s bottom line. This shift not only enhances operational resilience but also demonstrates a commitment to forward-thinking and responsible business practices. It’s not just about maintaining machinery; it’s about investing in the future of your company.
Benefits of Optimizing Preventive Maintenance
Optimizing preventive maintenance schedules is a game-changer for modern businesses, providing a myriad of benefits that extend beyond the immediate. Firstly, this approach maximizes the uptime of machinery, ensuring that it remains operational for longer periods without unplanned breakdowns. This continuity is critical in today’s fast-paced business environment, where even a minor hiccup can cascade into major operational setbacks.
Read Now : Timely Vehicle Service Reminders
Moreover, optimizing preventive maintenance schedules enhances the safety of the workplace. By addressing potential equipment failures before they arise, businesses mitigate risks that could lead to accidents or injuries. This proactive stance not only protects workers but enhances morale by demonstrating a commitment to safety and well-being. In turn, this can lead to higher retention rates and improved employee satisfaction.
In addition to these benefits, optimizing preventive maintenance schedules also fosters innovation. By freeing up resources and reducing unexpected expenses, companies can redirect their focus towards innovation and growth initiatives. This dynamic approach positions businesses at the cutting edge of their industries, enabling them to adapt swiftly to market changes and seize new opportunities. Ultimately, the decision to optimize preventive maintenance schedules is a strategic one, paving the way for sustained success and competitive advantage.
Understanding the Impact of Predictive Technologies
Harnessing the Power of Predictive Analytics
Predictive technologies are revolutionizing the landscape of maintenance by enabling businesses to not just respond to issues, but to anticipate them. The integration of predictive analytics into maintenance strategies is a cornerstone of optimizing preventive maintenance schedules. By analyzing data from various sensors and historical records, predictive technologies can forecast potential equipment failures with remarkable accuracy. This insight allows businesses to make informed decisions about when and how to perform maintenance, preventing unexpected downtimes and reducing operational interruptions.
The impact of predictive technologies is profound, offering businesses the ability to schedule maintenance activities with precision. As a result, companies can allocate their resources more efficiently, ensuring that investments in maintenance yield the maximum return. The adoption of predictive analytics thus transforms maintenance from a cost center into a strategic asset, driving business value and competitive advantage. Embracing these technologies is not merely an upgrade; it’s a strategic imperative for companies aiming to lead in efficiency and innovation.
Furthermore, the use of predictive analytics in optimizing preventive maintenance schedules supports a more sustainable business model. By preemptively addressing equipment vulnerabilities, businesses significantly reduce waste and extend the lifecycle of their machinery. This not only leads to financial savings but also aligns with environmentally conscious practices. As companies worldwide strive towards sustainability, the integration of predictive technologies in maintenance offers a pathway to achieving both ecological and economic goals.
Achieving Operational Excellence
To achieve operational excellence, integrating predictive technologies into your maintenance strategy is fundamental. The real-time insights provided by predictive analytics enable a level of precision in maintenance scheduling that traditional methods simply cannot match. Consequently, businesses experience fewer unexpected downtimes, enhanced equipment performance, and a robust bottom line. Optimizing preventive maintenance schedules is thus not just about maintenance; it’s a comprehensive approach to operational excellence, ensuring that every component of the business is performing at its peak.
Investing in predictive technologies as part of optimizing preventive maintenance schedules can also foster a culture of continuous improvement within an organization. As teams become adept at leveraging data for maintenance decisions, the organization as a whole becomes more responsive, agile, and competitive. The ripple effects of these advancements extend to every facet of the business, from customer satisfaction to financial stability. In this digital age, adopting predictive technologies is synonymous with staying ahead of the curve.
Lastly, the comprehensive data analysis and insights provided by predictive technologies empower businesses to refine and innovate their processes continually. This analytical capability enables companies to identify patterns and trends that may have gone unnoticed otherwise, facilitating informed strategic decisions. As part of a broader initiative to optimize preventive maintenance schedules, predictive technologies are an invaluable tool for achieving sustained operational excellence and creating a forward-thinking business ecosystem.
These narratives illustrate how crucial it is for modern businesses to embrace the optimization of preventive maintenance schedules. This approach transcends basic operational adjustments; it is a strategic, transformative journey toward heightened efficiency, safety, and innovation.